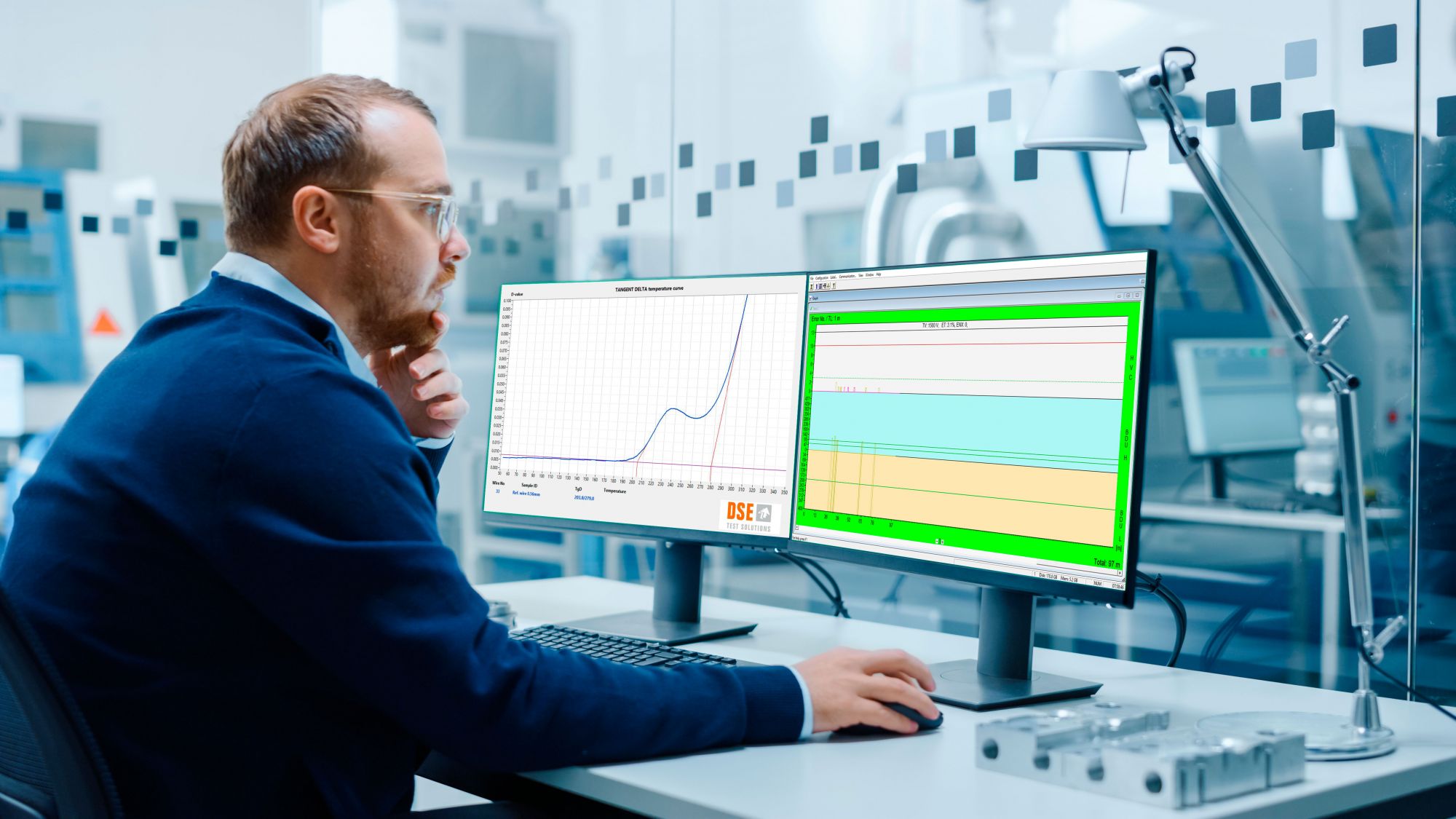
Test for curing, pinholes and blisters
We have reached a position as world market leader with our Tangent Delta instruments for curing control - our High Voltage Continuity Testers and BDU Testers for pinhole detection and blister detection. Our products are being used as reference instruments by manufacturers of enamel and enameled wire, as well as the users of enameled wire. To supplement our product range and to support our customers, we offer a wide range of training, maintenance and support activities.
Read more about Curing control, Pinhole test or Blister detection
Hairpin Tester for E-motors
With an increase of production of e-motors - our latest innovation is a tester of Hair Pins, which often are used in e-motors. An online test of each hairpin manufactured is being made - securing a high quality production.
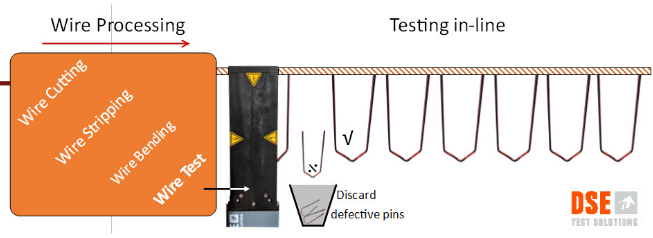
Market leader of wire testing products
Our extensive knowledge of the industry and customers allows us to collect information about the market needs and value of quality testing. Demonstrating more than 30 years of experience and global leadership with +50% market share, DSE Test Solutions is known as the most reliable supplier of high quality products and service.
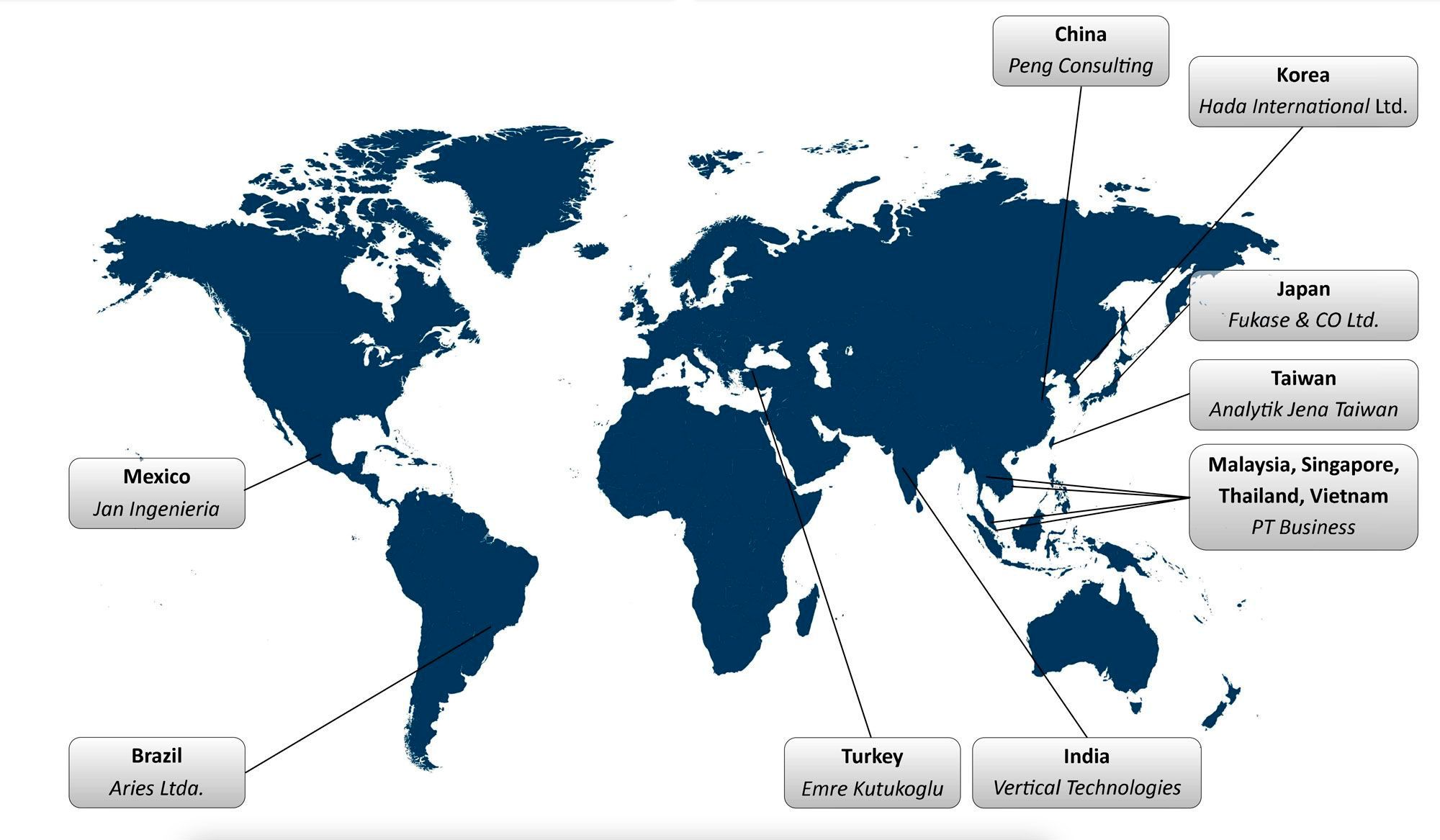
FAQ
What is enameled wire / magnet wire / winding wire?
Enameled wire, which is also mentioned as magnet wire, winding wire and sometimes insulated wire, is a highly versatile and useful material, used in numerous industries. In most cases it will be copper wire that is insulated, with typically one to four layers of polymer film. The insulation protects the wire from contact with its own and other wires’ electrical current, to prevent short circuits, and also to give the wire an advantage regarding its performance.
Do the mechanical properties of the wire, have anything to do with the curing of the enamel?
The enamel and the curing are very important, and it can be hard to document that the quality of the wire is approved, especially when you handle, bend, twist and winds the wire, in the production process.
The issues could be that the strength of the insulation will be lowered, which could cause short circuits. When testing the curing of the enamel with our Tangent Delta tester, you are provided with documentation proving that the residual solvents and curing state of the wire is approved. If these factors are not approved, it could have an unwanted influence on the temperature index, lifetime, and physical behavior of the wire.
What are the consequences of an under or over cured wire?
Under cured: Bad mechanical properties including too soft and unstable enamel. Usually, the amount of residual solvents will be too high. The tendencies for short circuits will be higher if the enamel is too soft.
Over cured: This enamel will be hard and “crispy”. When being handled in e.g. winding processes, the risk of cracking and breaking of the enamel will be higher, and the adhesion to the copper surface will be reduced.
What possibilities are there for testing and ensuring the quality of the wire?
As a result of DSE’s ongoing development of test equipment, the testing of the wire can take place before, during and after production.
The areas that DSE’s test equipment covers are curing of the insulation via Tangent Delta testers, in-line continuity test of wire and hairpins, and also blisters in the insulation with the help from DSE’s blister detection unit.
The possibilities are many and the test equipment can be implemented in countless ways – whichever fits the client the best.
What different test solutions does DSE develop and provide?
DSE Test Solutions’ lineup of products:
- Tangent Delta tester for curing control
- HVC Flex in-line tester for cracks, faults, pinholes, bare wire
- HVC Stand-alone tester – Individually, PLC or PC controlled, especially attractive for hairpin users
- BDU Blister Detection Unit, in-line blister detection for flat wire (Can be added to HVC lines)
What sizes and shapes of wire are possible to test?
The size and shape of wire is a deciding factor when it comes to choosing the correct wire testing solution. We at DSE, do our best to keep our products flexible and to cover the different sizes and shapes in the industry. Our equipment covers both flat and round wire – from sizes 0,005 mm to 26 mm including special hairpin electrode tops that covers the entire hairpin when testing it.
Is it possible for the test equipment to stop the production in case of too many errors?
The test equipment is developed with an eye on details, that will benefit the setup in which it is implemented. When e.g., installed in-line, the HVC/BDU will count errors and thereby alarm the operator and system, as soon as this threshold is exceeded.
The system also operates in test lengths and will provide documentation for the quality of the complete spool.
Does the curing affect the break down voltage of the wire?
The breakdown voltage will be at the highest level when the curing is correct.
How do I find out if DSE Test Solution’s test equipment would make sense for me?
Firstly, you start thinking about your production or use of enameled/magnet/winding wire. If your company is working with any type of wire and within the wire industry, we are confident that our test solutions will make sense in your setup.
With more than 30 years’ experience in the wire testing industry, we are always ready for a dialogue and exciting professional sparring, to help you determine and clarify where our testers would make sense in your company, please contact us at dse@dse.dk.